TRANSAIR: A REVOLUTIONARY SYSTEM FOR THE CORLET GROUP’S AIR SYSTEM
One of France’s major book printers, the Corlet Group has long been at the forefront of technological innovation and, since 1996, has systematically chosen Legris Transair® system when designing the air supply networks for its machines.
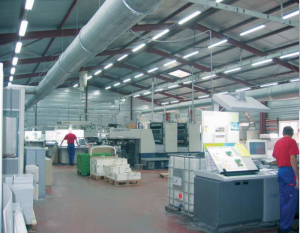
A NEGATIVE RESULT FOR TRADITIONAL PIPE TECHNOLOGIES
Galvanized steel and glued PVC pipes are still in existence at Corlet and present many disadvantages. The buildup of rust inside steel pipes makes air distribution less efficient and directly reduces print workshop productivity. Also, connecting traditional pipes remains complicated through the need for threading and welding. Installation of overhead take-offs and bleed point installation often takes excessive time.
Gluing time for PVC pipes can take more than 24 hours, with servicing carried out at the weekend and requiring the maintenance department to remain on stand-by. Gluing has to be completed on a Saturday morning so that the network can be pressurized on Sunday evening at the earliest… provided of course that gluing has been completely successful!
“Transair® is as simple as a
Meccano® set! Easy and quick to
assemble and disassemble and
completely versatile”
According to Mr. Jean-René Petit, Corlet Group’s maintenance manager, Legris Transair® system is really revolutionary in the air network field. He readily uses the image of a Meccano® set to highlight all of its advantages: an “easy and quick to assemble and disassemble, completely versatile” product.
“Transair® is as simple as a Meccano® set! Easy and quick to assemble and disassemble and completely versatile”
Aluminum pipes are very lightweight and easy to handle. Rapid-fit connectors save a considerable amount of time during assembly. As for Transair lugs, their small size and ease of assembly enable fast take-offs to the point of use. The connector range is well thought out. Valves allow individual pipe work to be isolated easily. Caps systematically fitted onto line ends ensure that future extensions can be made very quickly. Flexible loops compensate for level changes in the layout of the site, which is located on a hillside. The interchangeability of its components is another advantage of the Transair® system. Replacing a straight connector with a tee allows a drop to be fitted without cutting the pipe. Finally, immediate start-up after assembly or servicing the network allows the site to maintain high productivity.