THE VAL NANTAIS MARKET GARDENING COOPERATIVE CHOOSES TRANSAIR QUALITY
From the seed to the dinner table, quality is at the heart of Val Nantais’ success.For its compressed air system, the cooperative naturally chose the Legris Transair system.
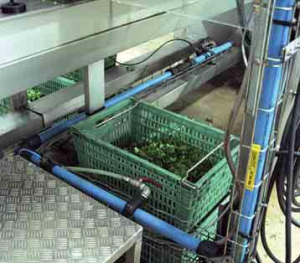
Val Nantais is a market gardening cooperative which currently brings together close on 100 vegetable producers. The total surface area under cultivation comes to 1,300 hectares. Freshly picked vegetables are taken to the washing and conditioning plant located close by. This houses two washing/degritting lines, four tray packing lines and two lines for the preparation of “ready-to-use” salad. These are integrated into 2.5 hectares of refrigerated premises with the ambient temperature and humidity adjusted for each type of vegetable.
On the logistical side, 12 loading platforms can deal with over 500 pallets on the ground at any one time and respond to orders in the most efficient manner possible. With a turnover approaching ?50m, of which 30% is for export, Val Nantais is currently France’s leading market gardening cooperative, able to meet the needs for fresh vegetables of 800 customers throughout the European Union and as far away as Eastern Europe. It was at Val Nantais that one of the very first Transair installations was completed in 1996
.
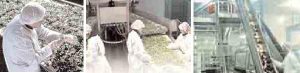
THE LIMITATIONS OF PVC
At that time, the preparation and conditioning plant was equipped with a plastic compressed air network. Weakened by large temperature swings, the pipe would often break under the effect of pressure. This plastic system had the added disadvantage of long assembly drying times and very little flexibility when alterations were made to the network for the addition of new lines and equipment, such as filters. To meet their exacting requirements, the attractive price of plastic could no longer be the only consideration and Val Nantais opted for the Transair system. The main compressed air feed columns were installed using 40mm diameter and then 63mm diameter pipe. Most of the drops were of 14 or 16mm flexible hose, connected directly to a quick assembly bracket fitted with a shut off valve.
The Transair system “does not require specific
Skills for installation or modification”
When Mr. Ragaud, the site maintenance manager, is asked about the Transair system, one of the major advantages he cites is that the system “does not require specific skills for installation or modification”.
In fact, since Val Nantais has been using the Transair system, extensions and modifications to the air network have been carried out by one of the eight staff making up the maintenance team. The pipe is easy to handle and to cut compared to galvanised steel pipe which takes much longer to cut to size and prepare because of the threading involved. With Transair, the pipe and brackets are ready to be assembled, leading to significant savings in installation times.
With Transair, it is simple
and quick to add to the network
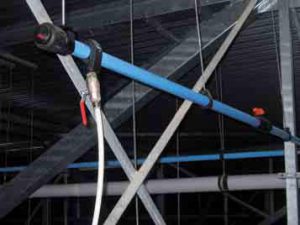
The bracket is just screwed onto a pre-drilled hole in he pipe, allowing a flexible hose to be connected. Numerous shut off taps are evenly spaced out in the ring main network, located in the roof-space. Mr Ragaud had realised that the original plastic installation did not have sufficient shut-off valves, a situation which had created problems when servicing the network. Thanks to the upgradeable Transair system, there was no problem in adding extra shut-off valves, enabling each section of the network to be isolated easily. A design software programme now available for creating drawing plans for further Transair installations has also proved beneficial for Val Nantais, enabling the network to be measured and product lists to be drawn up simply and quickly.