Cast Iron vs. Aluminum Piston Compressors
Piston compressors are the oldest and most common type of industrial air compressors, relying on the principle of positive displacement to increase the pressure of the enclosed volume of gas or air. While found in a wide variety of places, these compressors are most often in DIYers’ garages, hobby workshops, and full-service auto body and mechanic shops. They’re versatile – available in a variety of configurations, including single-acting, double-acting, oil-lubricated or oil-free. They’re economical – cheaper than rotary screw compressor technologies. And they’re sometimes portable – the utility infielder of the working world.
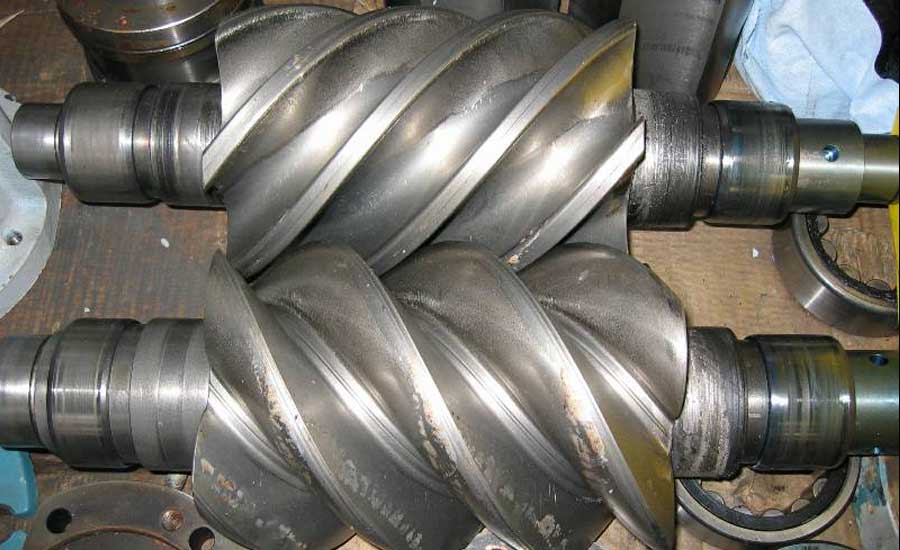
Piston Compressor Material Types
With a piston air compressor, the type of material involved refers to the metal used in the pump or shaft that surrounds the piston. These compressors are typically constructed of one of two materials – cast iron or aluminum. We’re going to give a quick breakdown of the differences between the two. First, let’s look at the characteristics of these two common and versatile materials.
Cast Iron Piston Compressors. Cast iron has excellent compressive strength, or the ability to withstand loads that would reduce its size. It is a perfect shock absorber! Piston compressors made of cast iron also have long service intervals and feature high cooling performance. Because it is very durable and much heavier than aluminum, cast iron is the perfect material for compressors that need to operate in heavy-duty environments and extreme conditions.
Aluminum Piston Compressors. Aluminum is low density and therefore low weight; it also has high strength, superior malleability, easy machining, excellent corrosion resistance, and good thermal and electrical conductivity. Its low density also makes it the ideal material for lightweight compressors that are easier to transport, install, and move around.
Is Cast Iron or Aluminum Better for My Application?
Ultimately, performance and durability are what matters the most. Mobility and ease of use are the other primary issues to consider. The general rule of thumb for choosing between aluminum and cast iron is this: if you need a small, flexible compressor that will be frequently moved from location to location, then aluminum is probably the material of choice. But if durability is most important to you, the compressor will be stationary, and it’s required to function reliably in tough conditions, then you will likely choose a cast iron model.
At Airpro Technix we provide complete Design, Installation & commissioning of the Compressed Air system.
? +92 310 5623329; +92 334 7980451
? info@airpro.com.pk