Compressed air in the flour mill is one of the systems needed to operate equipment in the plant. Appropriate design and installation of a compressed air system are often overlooked.
The most common use of compressed air is:
- to actuate air cylinders powering slide gates under bins
- to actuate outlets on conveying equipment.
- to open and close the doors under drop-bottom mixers.
These operations use the air in cyclic action where the cylinder(s) are used to position the gate(s) in either an opened or closed position. Other uses are to continuously operate vibrators on equipment or to atomize liquids by being injected into the liquid to atomize it before it is sprayed on the product.
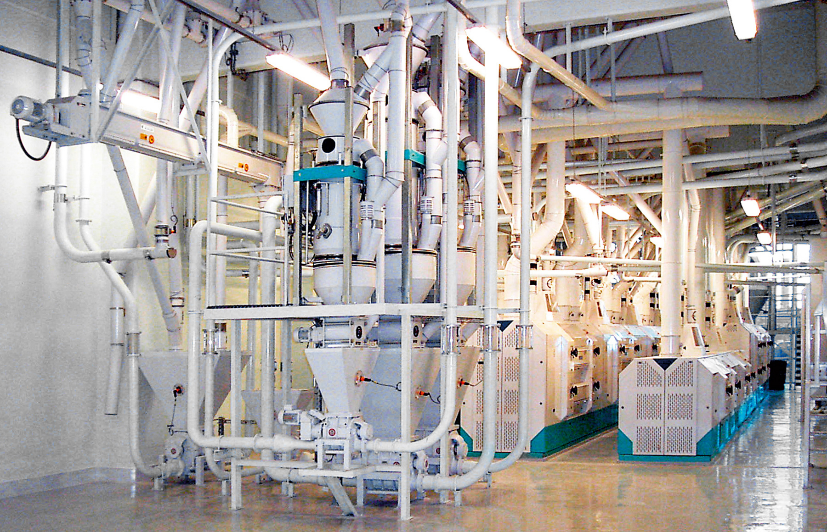
Major Components in Compressed Air System
A compressed air system has three major components:
- The compressor compresses the air.
- The compressed air distribution system.
- The equipment that uses compressed air.
The first point in the above mentioned is of high importance, Compressor and its downstream equipment is responsible for the longevity of the equipment that uses the compressed air.
Read More!
The air is compressed to the pressure needed for the plant compressed air system. The compressor has low and high-pressure switches on it. The low-pressure switch starts the air compression, while the high-pressure switch stops the air compression. The air is heated in the compression process and is hot as it leaves the compressor. This hot compressed air next passes through an air dryer to remove any moisture to provide the driest air possible to the system. The removal of moisture from the air is important as moisture in the air is detrimental to the piping system and the air-operated equipment.
The next step is the air receiver, which acts as an accumulation tank for the compressed air so that sufficient compressed air is available for the system when there is high demand.