Cost-Effective Engineering, Procurement & Construction (EPC) of Compressed Air Systems
Often referred to as the 4th utility after electricity, water, and gas, compressed air is the only major industrial power source generated on site by users bearing full financial and legal liability for its quality.
While the compressor is the largest energy-consuming component of your system, it is the usage, the overall design, and how well the system is maintained that determines the demand placed on the compressor and, therefore, its overall energy consumption.
Pressure losses can arise from poor system design, incorrectly dimensioned distribution piping and of course the purification equipment.
A thorough understanding of compressed air quality and testing standards is therefore indispensable when designing your system to achieve the purity levels your application requires. The International Organisation for Standardizations (ISO) sets three such standards, ISO 8573, ISO 12500, and ISO 7183. Which standards you should apply will depend on the specific contaminants you aim to remove and the purification equipment you will rely on to do so.
Pressure losses can arise from poor system design, incorrectly dimensioned distribution piping and of course the purification equipment.
To achieve the stringent air quality levels required for today’s modern production facilities, a careful approach to system design, commissioning and operation must be employed. Treatment at one point alone is not enough and it is highly recommended that the compressed air be treated prior to entry into the distribution system to a quality level suitable for protecting air receivers and distribution piping. Point of use purification should also be employed, with specific attention being focused on the application and the level of air quality required. This approach to system design ensures that air is not “over treated” and provides the most cost effective solution for high quality compressed air.
The following are examples of cost-effective compressed air system configurations:
Example configurations: Compressor room
A. With Adsorption Dryer and Oil Vapour Removal Filter
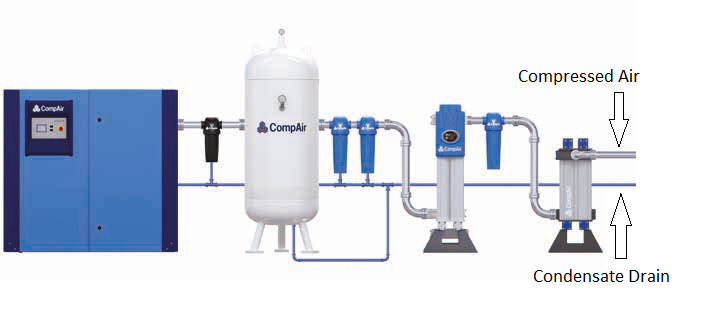
To Plant Ring Main
- ISO 8573-1:2010 Class 2.1.1
- ISO 8573-1:2010 Class 2.2.1
- ISO 8573-1:2010 Class 2.3.1
CLASS 0 for Total Oil
- ISO 8573-1:2010 Class 2.1.0 (<0.003 mg/m3 for total oil)
- ISO 8573-1:2010 Class 2.2.0 (<0.003 mg/m3 for total oil)
- ISO 8573-1:2010 Class 2.3.0 (<0.003 mg/m3 for total oil)
B. With Refrigeration Dryer
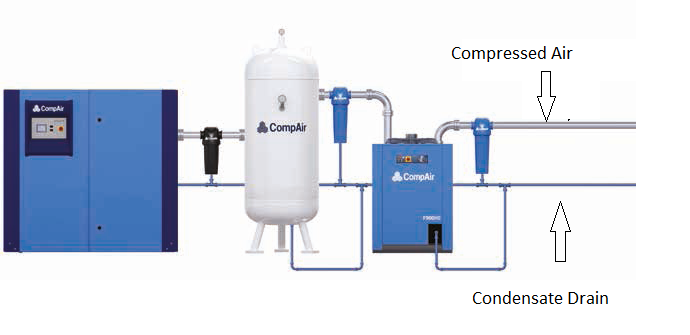
To Plant ring main
- ISO 8573-1:2010 Class 2.4.2
- ISO 8573-1:2010 Class 2.5.2

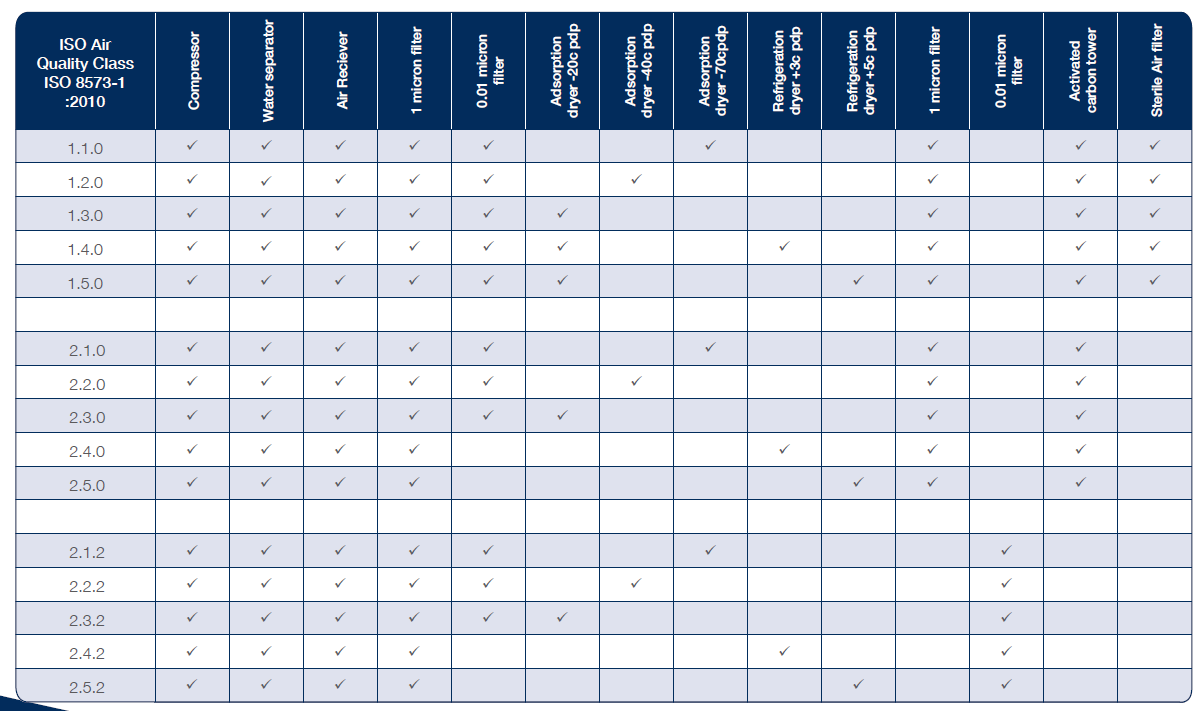
Example configuration: Critical applications
A + C, D or E
B + F or G
Typical Applications:
- Pharmaceutical products
- Silicon wafer manufacturing
- TFT / LCD screen manufacturing
- Optical storage devices (CD, CD/RW, DVD, DVD/RW)
- Optical disk manufacturing (CDs/DVDs)
- Hard disk manufacturing
- Foodstuffs
- Dairies
- Breweries
- CDA systems for electronics manufacturing
- Blow molding of plastics e.g. P.E.T. bottles
- Film processing
- Critical instrumentation
- Advanced pneumatics
- Air blast circuit breakers
- Decompression chambers
- Cosmetic production
- Medical air
- Dental air
- Lasers and optics
- Robotics
- Spray painting
- Air bearings
- Pipeline purging
- Measuring equipment
- Blanketing
- Modified atmosphere packaging
- Pre-treatment for on-site gas generation
Example configuration: General Usage
B + C, D or E
Typical Applications:
- General ring main protection
- Pre-filtration to point of use adsorption air dryers
- Plant automation
- Air logistics
- Pneumatic tools
- General instrumentation
- Metal stamping
- Forging
- General industrial assembly (no external pipework)
- Air conveying
- Air motors
- Workshop (tools)
- Garage (tyre filling)
- Temperature control systems
- Blow guns
- Gauging equipment
- Raw material mixing
Who to Call in Pakistan for Cost-Effective Compressed Air System Design?
AirPro Technix has been delivering Cost-Effective Turnkey Compressed Air Systems with Construction, Engineering and Procurement (CEP) services in Pakistan. With a team of experienced compressed air engineers providing energy efficient solutions, our concentration is on modern, innovative, energy-efficient compressed air system.
Important note:
Equipment recommendations are identical for both oil-free and oil lubricated compressors.
The requirement for both breathable quality air is not covered in ISO 8573.1. Refer to breathing air standards for the country of installation.