Energy Savings using Aluminium Piping system
Compressed air represents one of the largest opportunities for immediate energy savings, which is on average 15% of any industrial facility’s consumption of electricity. If the pipe system itself is not designed for compressed air, there is a good chance that much of the costs associated with commissioning the system and producing compressed air are wasteful and unnecessary.
Optimizing and controlling the production of compressed air is an opportunity to make immediate energy savings.
Over a ten-year period, the cost of energy consumed by an average compressed air system exceeds other costs, including the initial cost of equipment and installation.
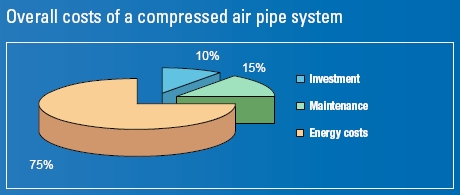
With 75% of the cost of a compressor due to energy use, significant cost savings will be made by improving energy efficiency, as well as the added benefits of improving the performance of your system and reducing your organisation’s ‘carbon footprint
The potential savings (payback time of fewer than 36 months) can be summarized in three main categories in terms of potential contribution. ,
- Reducing Air Leaks
- Improving/Adding More Compressors
- Global pipework system improvement
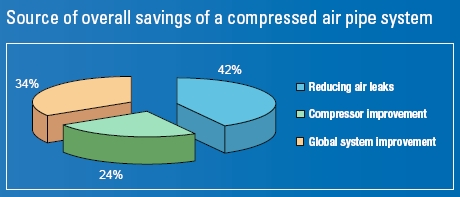
With reference to the image above, reducing air leaks is the greater potential to improve the efficiency of a network, but improving a pipework system also gives potential cost savings of 34%.
Parker’s Transair aluminum pipe system significantly reduces plant energy costs by increasing efficiency, reducing pressure drops, and eliminating leaks. Unlike the performance of steel and copper, which degrades over time due to corrosion, Transair provides clean air quality with optimum flow rate performance.
Have questions or need a quotation?