Managing Compressed Air Risks in Pharmaceuticals Production in Pakistan
Many compressed air processes in pharmaceutical manufacturing facilities in Pakistan operate continuously around the clock. As such, it’s critical that any potential risks are managed appropriately.
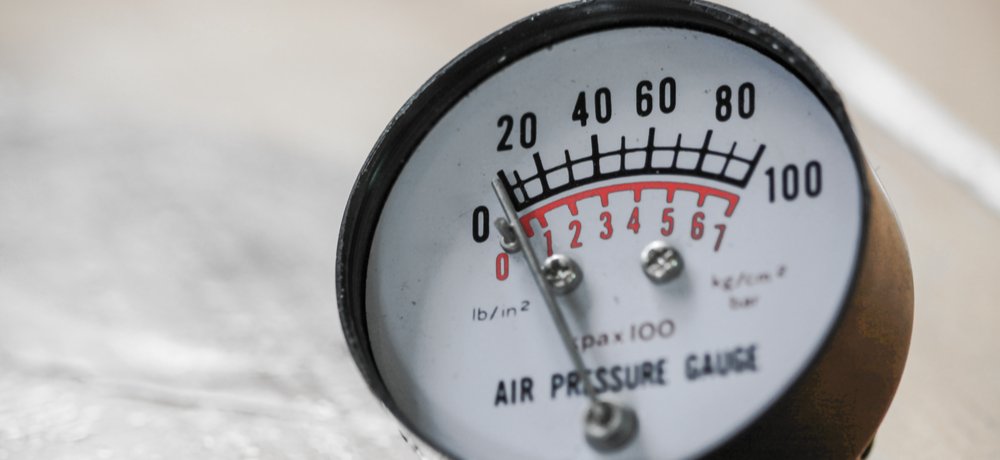
The pharmaceutical industry is one of the most highly regulated in Pakistan. But while these regulations cover even the smallest technical aspects of pharmaceutical production, they pay comparatively little attention to the use of compressed air in manufacturing processes.
From laboratories to extruders, bottling plants, tablet presses and packaging processes, compressed air is used in a range of pharmaceutical applications. And in many of these processes, compressed air will come into direct contact with products. This might be drying equipment parts, transporting substances through tubes, or using compressed air as a pressure blanket for solutions in tanks. Nevertheless, many of these processes operate 24/7, so ensuring the right compressor is specified is critical.
When a new system is designed and specified, the regulatory basis for the use of compressed air is provided by the contract manufacturer and/or the pharmaceutical company. Understandably, a risk analysis and assessment needs to be undertaken to help stop any issues arising, or at least ensure all possible steps have been taken to minimise any potential problems.
This will include whether the compressed air application involves direct or indirect contact with products, the volumes of compressed air required, and whether the manufactured product is a sterile medicine or microbiologically unstable. Other questions that need to be asked include whether any other potential contaminants associated with a compressed air system – such as particles or oil – must be taken into account, and whether the product being manufactured is sensitive to moisture.
Controlling Contaminants
Particles from contaminants in compressed air can potentially stop a pneumatic system from performing as expected and could even lead to production quality issues further down the line. This is a particular risk if the process air comes into contact with the goods being manufactured.
- The intake air in a compressor is susceptible to contamination from almost any kind of particles – from pollen, dust and hydrocarbons to heavy metals such as lead, cadmium or mercury. Crucially, many fail to take into account how particle concentrations in a system increase when compressed air is generated.
- There is the very real danger that blow-off air from a pneumatic system may come into direct contact with a product.
- Another concern is that a pharmaceutical company may inadvertently introduce errors at the specification stage, by not undertaking a comprehensive enough review of what’s required from a compressed air system.
Because of the lack of regulations surrounding compressed air usage in the pharmaceutical sector in Pakistan, it falls to compressed air supplier like Rastgar Air Compressors in Pakistan and pharmaceutical companies to decide what the appropriate air quality standards that a system needs to meet is.
- Furthermore, a poorly designed compressor and pipework can have serious consequences, resulting in significant costs to remedy further down the line. Pipework leaks, for instance, are the leading cause of energy loss in industrial air systems, potentially wasting as much as 20-30% of a compressor’s output
Opportunities with Oil-Free Compressors
When it comes to meeting air purity demands for a pharmaceutical manufacturing environment, there are a range of options available to help achieve this.
- Oil-lubricated models use filtration systems, and these can provide the right standard of compressed air needed for these sites. However, these rely on oil separator elements and downstream filters being replaced, which adds to on-going costs.
- Alternatively, there is the option of oil-free technology. By its very design, this technology is focused on keeping oil particles out of the compressor and can offer a whole host of benefits, particularly for pharmaceutical manufacturing sites that only need a starting pressure of 10 bar. With few pharmaceutical production processes requiring high pressure levels, then an oil-free system could offer an ideal solution for many facilities.
Oil-free systems use a range of technologies that bypass the need for oil. While oil-lubricated compressors use oil in the compression chamber to cool and seal the compressed air generated, oil-free technology eliminates this risk of contamination while delivering guaranteed air purity.
When choosing an oil-free compressed air system, there are a number of different technologies to choose from. Whether it’s scroll technology, which consists of an orbiting, rotating scroll and fixed scroll housing, which together create compression chambers, or water-injected rotary screw products, which use water to lubricate, seal and cool the compression process, or two-stage dry screw compressors, the best solution will depend on a site’s needs and demands.
Oil-free technology can also help energy managers make valuable cost savings while improving operational efficiencies too. Whole life costs are reduced, with businesses able to save on the cost of oil replacement. Unlike oil-lubricated systems that require oil change intervals throughout their service life, there is also no need to purchase equipment that would clean and separate oil from air, such as oil separators, filtration equipment and condensate treatment.
Another benefit to consider with oil-free technology is that, with many businesses faced with ambitious sustainability goals, deciding on an oil-free solution provides the most eco-conscious choice too, helping to contribute towards a facility’s green credentials.
Future-Proofing A Facility
Air purity is crucial for many industries, but in no industry is this truer than the pharmaceutical sector. For businesses in Pakistan that want to be assured that contamination is eliminated from their compressed air processes, oil-free can deliver a real range of benefits.
Ultimately, the diversity of compressed air applications used in pharmaceutical environments is huge, and when it comes to regulating compressed air in this industry, it is debatable whether any unifying standards will be drawn up in future. As a result, decision makers must pay time and attention on setting the standard for this sector.
For Selection, Design, Procure, Install, Commission ISO 8573 compliant compressed air system for Pharmaceuticals plants in Pakistan,