Over the last 100 years, manufacturing has been enhanced by the introduction of compressed air in the assembly line to increase worker’s safety and the overall efficiency of the manufacturing plant. It is used as a tool in almost every step in the process of manufacturing from painting, cleaning, engine, and assembly.
Paint Application, primer coats, base coats, and finishing clear coats, all consume compressed air. As a result, compressed air plays a critical role in the paint industry, so the choice of air compressors should be considered carefully.
Negative results when compressed air is not clean.
Oil Can:
- Prevent paint adhesion to surfaces
- Paint to crack, flake, or bead
- Create future corrosion or the final finish on a car
Water Can:
- Cause negative visual and textural effects on the finish: spotting or “fish-eyes”
- Stick to pipe walls
- Collect in the receiver when the air velocity reduces
- Squirt out of the nozzle with the compressed air
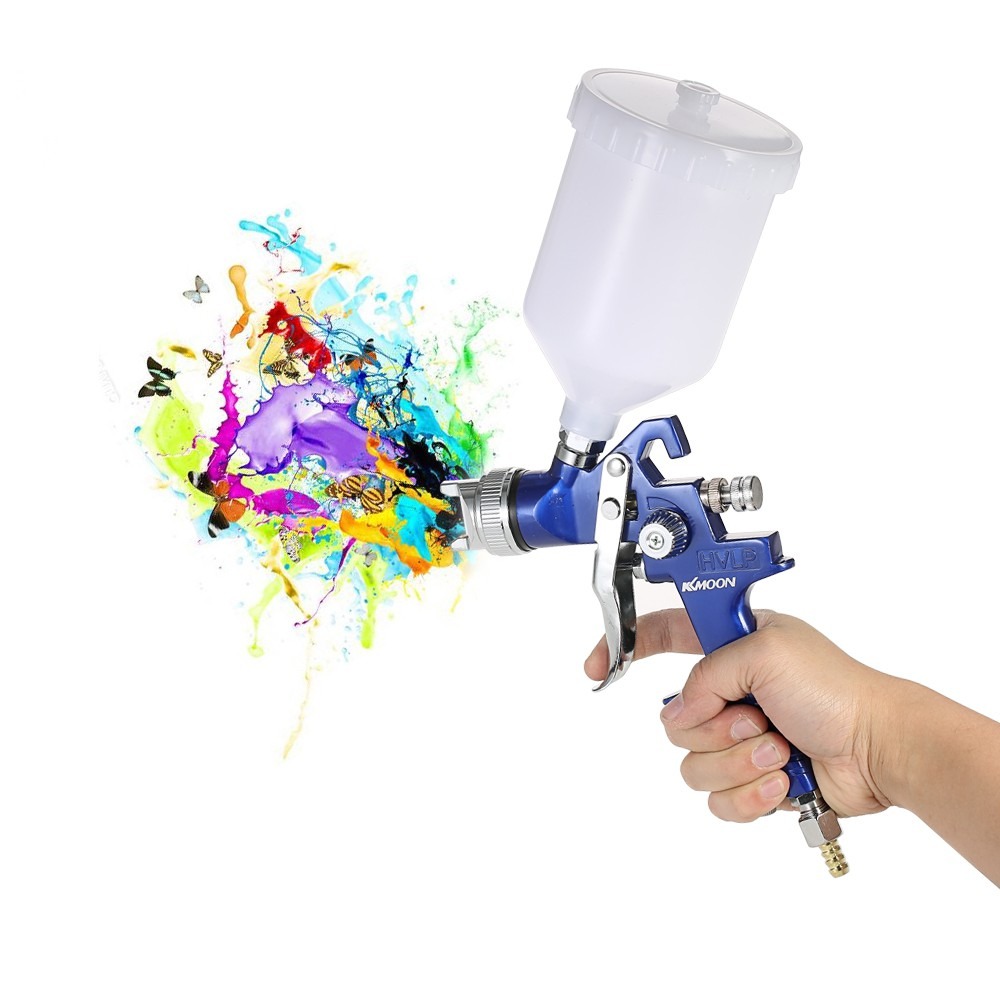